Damages and preventive measures of water well drilling
Drilling for water wells is a significant process for obtaining groundwater resources. Proper execution and adherence to preventive measures ensure the safety of the environment, equipment, and personnel involved. Here's a breakdown of potential issues during water well drilling and the affirmative steps taken to prevent them:
Environmental Protection is a Priority
1. Groundwater Pollution is Prevented:
Drilling fluids, lubricants, fuel, and waste are handled correctly to prevent leaks and seepage into underground water sources, thus ensuring water remains clean and safe for drinking and agriculture.
Environmentally sound drilling fluids and lubricants are utilized.
A robust waste collection and disposal system is in place to prevent indiscriminate discharge.
Equipment is well-maintained to avoid oil leaks.
Effective sealing measures are implemented when drilling through different underground water layers to prevent cross-contamination.
The wellhead is securely sealed upon completion of drilling.
2. Surface Water Pollution is Controlled:
Mud, rock cuttings, and wastewater from drilling are managed to prevent direct discharge into surface water bodies, thereby avoiding increased suspended solids and turbidity that harm aquatic life and water functionality.
Proper mud pits and settling ponds are constructed to treat mud and wastewater for compliant disposal or reuse.
Measures are taken to prevent rainwater runoff from the drilling site carrying pollutants into surface water.
Protective barriers are set up when drilling near surface water to prevent contaminants from splashing in.
3. Soil Contamination is Avoided:
Leaks of drilling fluids, oil, or waste are prevented from polluting the soil around the drilling site, thus protecting soil quality and plant growth.
Impermeable liners are laid on the drilling site to prevent pollutants from seeping into the soil.
Regular checks and maintenance of equipment and pipes prevent leaks.
Drilling waste is promptly cleaned up and disposed of.
Contaminated soil is remediated after drilling is completed.
4. Land Use and Vegetation are Respected:
Drilling sites are planned carefully to minimize land occupation and prevent the destruction of existing vegetation, thereby safeguarding the ecological environment.
Drilling sites are planned rationally to minimize the occupied land area.
Vegetation around the drilling site is protected, and measures are taken to reduce damage.
The site is promptly leveled, and vegetation is restored after drilling.
5. Noise Pollution is Mitigated:
The operation of drilling equipment is managed to reduce noise impact on nearby residents and wildlife habitats.
Quieter drilling equipment and methods are selected.
Sound barriers or other noise reduction measures are implemented.
Drilling schedules are planned to avoid high-noise activities at night or during sensitive times.
Equipment Integrity is Maintained
1. Wear and Tear of Drill Parts are Managed:
Proper techniques and equipment are used to minimize wear, bending, or breakage of drill bits and pipes when drilling through hard rock, ensuring efficient and safe drilling.
Appropriate drill parts are selected based on the geological formation.
Reasonable drilling pressure and rotation speed are controlled.
Drill parts are regularly inspected and maintained, with worn or damaged components promptly replaced.
Equipment is operated correctly to avoid strong impacts and undue stress.
2. Drill Rig Functionality is Ensured:
Regular maintenance and trained operation prevent breakdowns of the engine, hydraulic system, transmission, and other parts of the drill rig, minimizing delays and ensuring continuous work.
A comprehensive equipment maintenance schedule is established, including regular checks, lubrication, and upkeep.
Equipment operators are professionally trained and familiar with the equipment's performance and operating procedures.
Potential equipment issues are addressed promptly to prevent minor faults from escalating.
3. Wellhead Equipment Safety is Guaranteed:
Proper installation and operation of wellhead equipment, such as the derrick and pulleys, prevent tilting, deformation, or collapse, thus avoiding serious accidents.
Installation and commissioning of wellhead equipment strictly follow regulations.
The stability and connections of wellhead equipment are regularly inspected.
Operators are familiar with the operating procedures and safety precautions for wellhead equipment.
Overloading operations are avoided.
Personnel Safety is Paramount
1. Injuries from Machinery are Prevented:
Moving parts, falling objects, or flying debris from drilling equipment are controlled to prevent crushing, hitting, or cutting injuries to workers.
All personnel on site wear certified personal protective equipment (PPE), including hard hats, safety boots, goggles, and gloves.
Thorough safety education and training are provided to enhance workers' safety awareness and operating skills.
Comprehensive safety protection facilities, such as protective covers and safety warning signs, are installed.
Standard operating procedures are enforced to ensure personnel maintain a safe distance from hazardous areas.
2. Falls from Heights are Prevented:
Safety measures are strictly enforced when working on the derrick to prevent falls from high elevations.
Safety harnesses are mandatory and correctly worn when working at height.
Stable work platforms and safe access routes are provided.
The safety of high-altitude work equipment is regularly inspected.
Risky activities at height are prohibited.
3. Electrocution is Avoided:
Electrical equipment and wiring on the drilling site are managed safely to prevent electric shock incidents.
Electrical safety regulations are strictly adhered to.
The insulation of electrical equipment and wires is regularly checked.
Certified electrical equipment and tools are used.
Only qualified electricians handle electrical equipment.
4. Poisoning and Suffocation are Prevented:
Potential exposure to hazardous gases (like hydrogen sulfide) or work in poorly ventilated areas is managed to prevent poisoning or suffocation.
Hazardous gas monitoring is conducted in work environments.
Necessary protective equipment, such as gas masks and respirators, is provided.
Ventilation is enhanced to ensure good airflow in work areas.
Emergency rescue drills are conducted regularly.
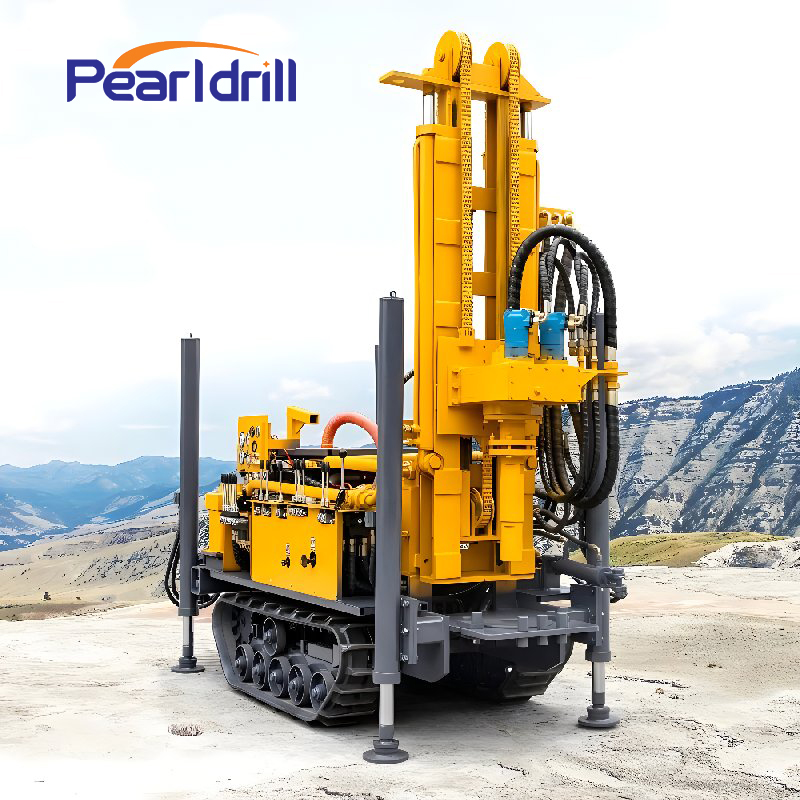
If you don’t know how to select the right water well drilling rig, click the link below to contact our professional team directly.