How to handle a stuck drill pipe in water well drilling?
Drilling a water well is a complex process, and encountering a stuck drill pipe is a common challenge. Here are some common solutions:
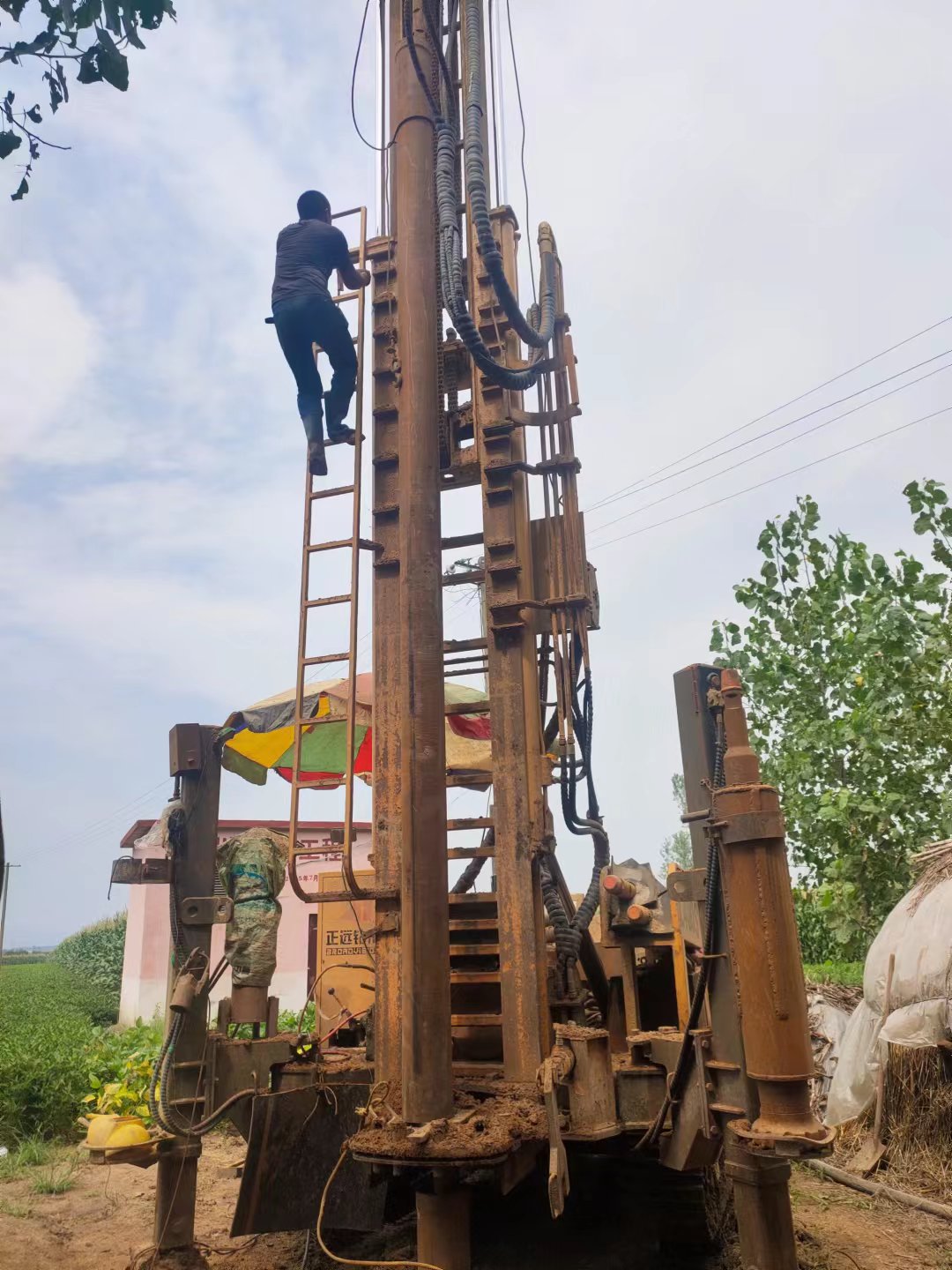
I. Analyzing the Causes of a Stuck Pipe
Geological Factors
-
Cause: Complex geological formations, such as caves or fractured strata, can cause a drill pipe to become stuck. When a drill pipe enters a cave, it might get lodged due to fillings like clay or rock fragments. In fractured strata, the drill pipe can wedge into a fracture.
-
Another common cause is formation expansion. For instance, in strata with high clay content, water can cause the clay to swell, exerting pressure on the drill pipe and causing it to get stuck.
-
Identification: Monitor changes in drilling parameters. A sudden change in drilling pressure, increased torque, and abnormal circulation (e.g., reduced or no return flow) may indicate a geological cause.
Operational Errors
-
Cause: Excessive drilling speed is a significant factor. If the drilling speed exceeds the permissible rate for the formation, excessive cuttings can accumulate around the drill bit, causing it to get stuck.
-
Rough handling of the drill pipe when tripping can also lead to a stuck pipe. For example, rapidly pulling up the drill pipe can increase friction between the pipe and the borehole, causing it to get stuck.
-
Identification: Review drilling records. If the drilling speed was significantly higher than the recommended rate for the formation and the stuck pipe occurred while the Mud Pump pressure was normal and circulation was good, excessive drilling speed is likely the cause. If the stuck pipe occurred during tripping, the operator would usually feel a sudden increase in resistance.
Poor Mud Properties
-
Cause: Improper mud viscosity and density. If the mud viscosity is too low, it cannot effectively carry cuttings, leading to their settling. If the density is too low, it may not balance the formation pressure, causing borehole collapse and a stuck pipe. Conversely, excessive density can increase the buoyancy of the drill pipe, hindering its normal descent.
-
Excessive mud loss can also be problematic. When there is excessive mud loss, a thick mud cake forms on the borehole wall, reducing the borehole diameter and causing the drill pipe to get stuck.
-
Identification: Test the mud properties. If the viscosity, density, or fluid loss is outside the recommended range for the formation and there's a stuck pipe, poor mud properties are likely the cause.
II. Solutions for a Stuck Pipe
1. Moving the Drill Pipe
-
Procedure: Initially, try to move the drill pipe up and down slightly. While ensuring the safety of the drill pipe, slowly pull up and push down on the pipe. The upward force should be gradually increased, with each movement limited to a small distance (e.g., a few centimeters to a few inches). Observe whether the drill pipe can be freed. This method is suitable for minor sticking, such as slight friction between the drill pipe and the borehole wall or a small amount of accumulated cuttings.
-
Precautions: Closely monitor the force on the drill pipe using a weight indicator. Avoid excessive force to prevent breaking the drill pipe. Maintain mud circulation to effectively remove cuttings and other obstructions around the drill pipe.
2. Circulating Mud
-
Procedure: Adjust mud properties and circulate. If the stuck pipe is caused by poor mud properties, improve the mud properties first. For example, if the viscosity is too low, add a viscosifier; if there is excessive fluid loss, add a fluid loss control agent. Then, start the mud pump and circulate the mud at an appropriate rate and pressure to flush the cuttings and other blockages around the drill pipe. Circulation time may vary and can last for several hours or even longer.
-
Precautions: Monitor the mud pump pressure to avoid excessive pressure that could cause borehole fractures. Ensure that the mud properties are adjusted appropriately to avoid exacerbating the stuck pipe condition.
3. Vibration Method
-
Procedure: Use a specialized vibration tool, such as a hydraulic vibrator. Connect the vibrator to the drill pipe and generate upward or downward impact forces to vibrate the stuck section and loosen the drill pipe. The intensity and frequency of the vibration should be determined based on the specific stuck pipe situation and the strength of the drill pipe.
-
Precautions: Before using the vibrator, inspect the connections of the drill pipe to ensure they are secure to prevent the drill pipe from breaking during vibration. Adjust the vibration force based on the material and specifications of the drill pipe to avoid damage.
4. Reverse Circulation and Underreaming (for complex situations)
-
Procedure: If other methods fail to resolve the stuck pipe, reverse circulation and underreaming can be considered. First, reverse the circulation and pull the drill pipe out of the stuck section. Then, use an underreaming tool, such as an underreamer, to cut through the obstacles surrounding the stuck drill pipe. The underreamer rotates and cuts away the cuttings, collapsed formation, etc., freeing the stuck drill pipe.
-
Precautions: Accurate calculation of the reverse circulation torque is required to prevent the drill pipe from breaking at other sections. During underreaming, control the rotation speed and feed rate of the underreamer and maintain good mud circulation to remove the cuttings produced by underreaming. This is a relatively complex and high-risk method that requires experienced operators.