How to prevent water well drilling rig failure
In order to prevent water well Drilling Rig failure, you can start from the following aspects:
1. Daily maintenance and upkeep:
Check the drill rods and bits: check the wear of drill rods and bits every day, and replace them in time when they are found to be seriously worn, so as to avoid affecting the drilling efficiency and hole wall quality.
Clean the Mud Pump: The mud pump is an important part of the drilling rig, the sealing and wear of the pump should be checked regularly, and the mud pump should be kept clean to prevent the impurities in the mud from clogging the pump body.
Replace the lubricating oil and filter: According to the requirements of the instruction manual of the equipment, regularly replace the lubricating oil in the main engine, gearbox, hydraulic system, etc., and replace the filter to prevent damage to the equipment caused by aging of the oil or accumulation of impurities.
Check and tighten the connecting parts: Regularly check the connecting parts of the drilling rig, especially the bolted connections of the drilling tower, rotary mechanism and mud pump, and tighten the loose bolts in time to prevent loosening or breakage caused by vibration.
Clean the drilling rig: Clean the drilling rig regularly to remove mud, sand and other debris, keep the equipment clean and prevent debris from affecting the normal operation of the equipment.
Attention to lubrication: Add lubricant to each part in time to keep the equipment running smoothly.
2. operation standardization:
Check before starting: Before starting the machinery and equipment should be checked before the coolant and oil is enough, insufficient to timely replenish before starting.
Preheating: start to enter a low-speed warm-up phase, until the coolant and oil to reach the specified temperature, and then start working, is strictly prohibited under low temperature overload operation.
Reasonable operation: When drilling, choose the appropriate rotational speed, feed speed and pressure, and maintain a stable drilling speed and drilling force to prevent the quality of drilling from deteriorating due to damage to the drill bit and clogging. When swinging the drill pipe, the speed of the lens needs to be slowed down to avoid offset or displacement of the pile hole and damage to the drill pipe.
Pay attention to the geological conditions: Before excavation, the construction site should be surveyed to determine the geological conditions and drilling location, and the construction plan should be formulated to avoid drilling offset or damage to the equipment due to improper construction.
3. Lubrication management:
Reasonable lubrication: According to statistics, more than 50% of the wear and tear failure of mechanical equipment is caused by poor lubrication of mechanical operation system. Good lubrication can maintain its normal working gap and appropriate working temperature, prevent dust and other impurities from entering the machinery, thereby reducing the wear and tear of parts and reducing mechanical failure.
Select the appropriate lubricant: not arbitrary substitution, not the use of shoddy products.
Regular inspection: we should always check the quantity and quality of lubricants, insufficient quantity should be supplemented, poor quality should be replaced in a timely manner.
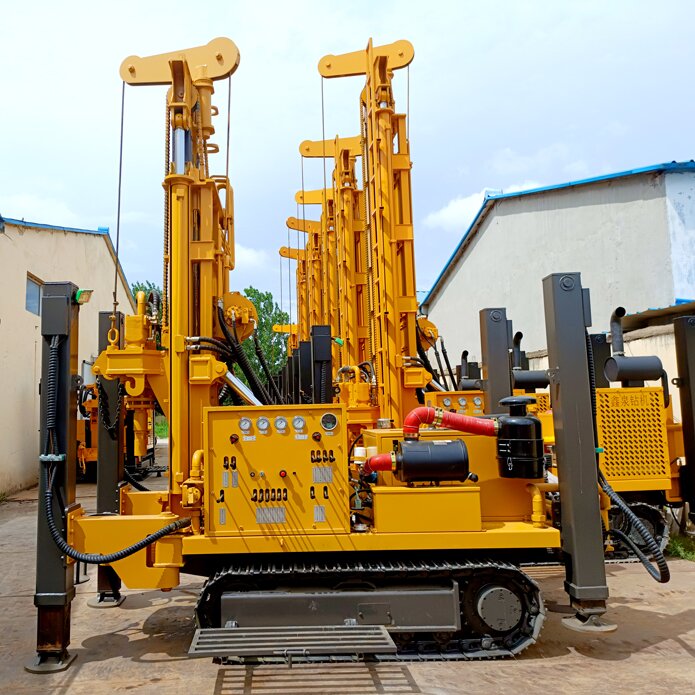
Summarize:
Through the above measures, we can effectively prevent water well drilling rig failures, improve drilling efficiency and extend the service life of the equipment. In short, prevention is the mainstay, maintenance is supplementary, and standardized operation can minimize the occurrence of failures.
If you need to buy the right water well drilling rig, click the link below to contact our professional team.
Contact us