What is the difference between centrifugal pump and slurry pump?
Centrifugal pumps and slurry pumps are both types of pumps used to move fluids, but they differ in their specific applications and designs. Here are the key differences between the two:
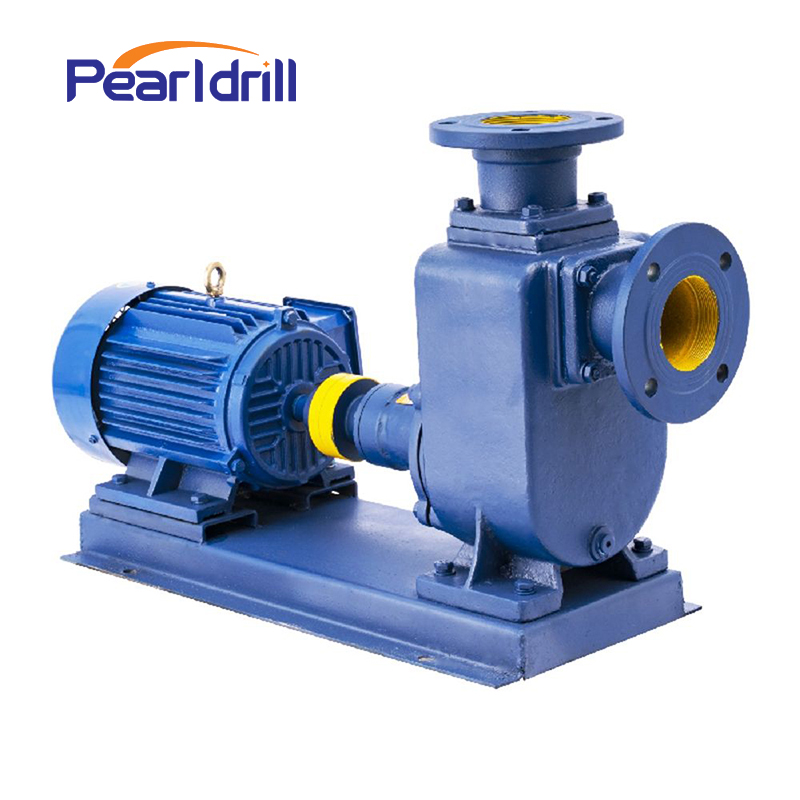
1. Application: Centrifugal pumps are primarily used to transport clean or low-viscosity fluids, such as water, chemicals, and petroleum products. They are commonly employed in industries like water supply, HVAC systems, and irrigation. On the other hand, slurry pumps are specifically designed to handle abrasive and high-viscosity fluids, known as slurries. Slurries consist of solid particles suspended in a liquid medium and are commonly found in mining, construction, dredging, and other industries where heavy-duty pumping is required.
2. Design and Construction: Centrifugal pumps have a relatively simple design, comprising an impeller that rotates on a shaft within a casing. The impeller imparts centrifugal force to the fluid, propelling it outward and creating pressure that moves the fluid through the system. Slurry pumps, in contrast, are built to withstand the harsh conditions associated with pumping abrasive slurries. They typically feature robust construction with heavy-duty materials, including hardened alloys, to resist wear and erosion caused by the solid particles in the slurry.
3. Impeller Design: The impeller design differs between centrifugal pumps and slurry pumps. Centrifugal pumps usually have closed or semi-open impellers that are efficient in moving clean liquids. Slurry pumps, on the other hand, often have open or recessed impellers with wider vanes and larger passageways to accommodate the passage of solid particles without clogging or excessive wear. This design allows slurry pumps to handle the high-concentration solids present in slurries.
4. Shaft Seal: Centrifugal pumps typically use various types of shaft seals, such as mechanical seals or gland packing, to prevent fluid leakage along the shaft. Slurry pumps, due to the abrasive nature of the transported slurry, often employ specialized sealing mechanisms, such as gland packing with lantern rings or mechanical seals with added features for improved wear resistance.
5. Performance: Centrifugal pumps are generally designed for high flow rates and moderate-to-high pressures. They are optimized for efficient operation when handling relatively clean liquids. Slurry pumps, on the other hand, are designed to handle lower flow rates but with higher pressures due to the higher viscosity and resistance posed by the solid particles in the slurry. Their performance is focused on maintaining reliability and durability in challenging slurry pumping applications.
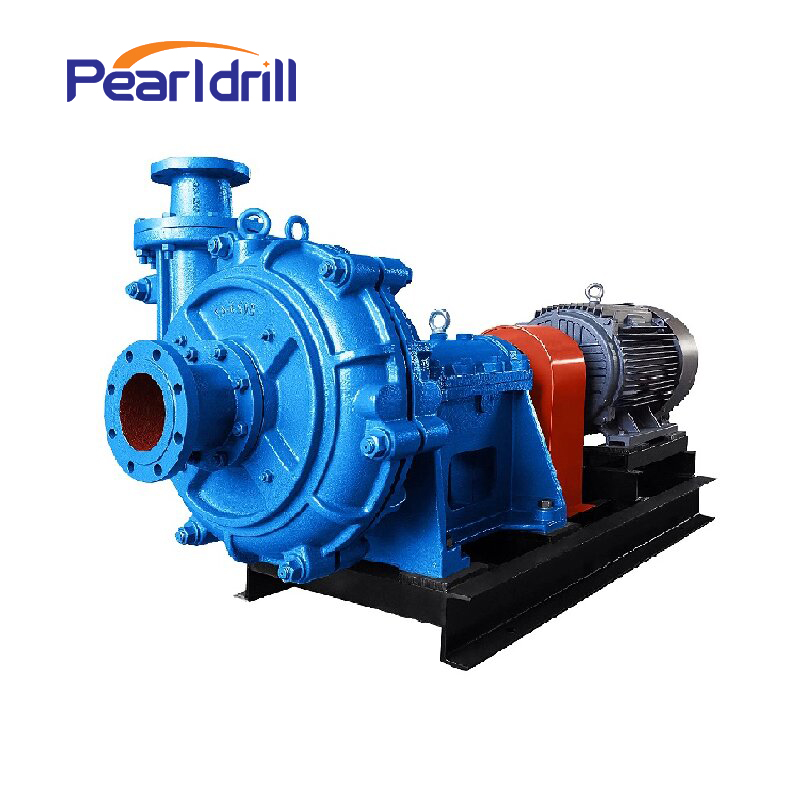
In summary, centrifugal pumps are suitable for clean or low-viscosity fluids, while slurry pumps are specifically designed to handle abrasive and high-viscosity slurries. The differences in design, impeller construction, shaft sealing, and performance make them tailored for their respective applications.